Epoxy is no longer the leading choice for garage floor coating systems; polyaspartic coatings are more durable, attractive, and are extremely affordable. Learn more about why polyaspartic is superior to epoxy floor coatings below!
Polyaspartic Floor Coatings
Better than Epoxy
Polyaspartic: If it’s not done in 4, it’s not a Garage Cave floor!
Four Times Stronger Than Epoxy
- Withstands hot tire pick up
- Extremely customizable
- Impervious to chemicals
- Prep & install in as little as four hours
- Color will not fade or yellow
FC-USA Poly Supreme Polyaspartic Coatings
A garage is a haven for many people. With FC-USA polyaspartic coatings, you can choose the look that fits you and your décor. By varying the combination of color flakes and chip size, our applicators can achieve just about any appearance for your garage floor coating. One great way to achieve this is with our beautiful, durable garage floor coatings, expertly installed by Your Garage Cave’s qualified floor technicians. FC-USA polyaspartic coatings lead the seamless resinous concrete floor coatings industry by outperforming and outlasting other polyurea, polyaspartic, and epoxy floors nationwide.
Polyaspartic Floor Coating vs. Epoxy
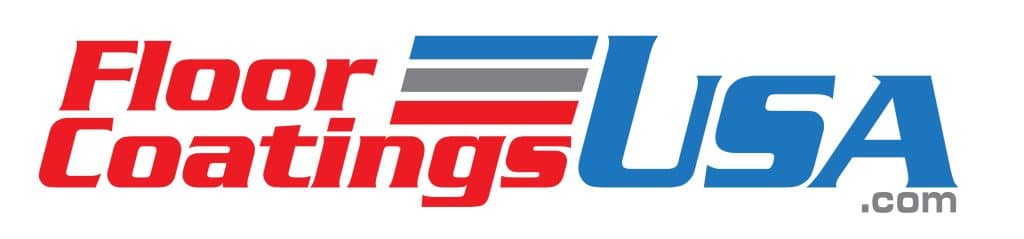
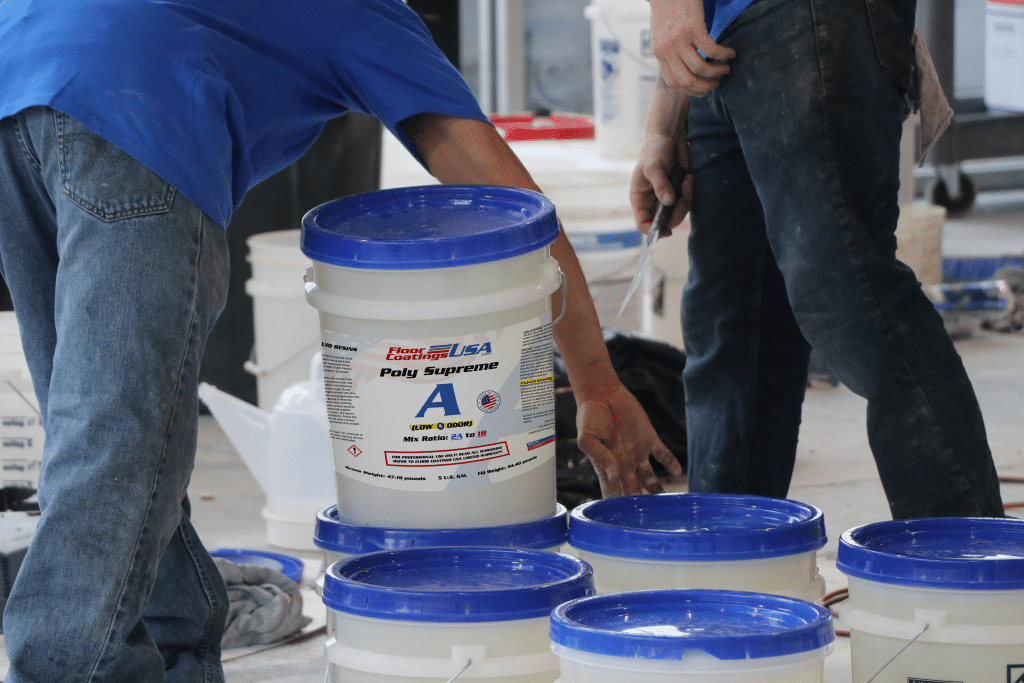
How does FCUSA Polyaspartics stack up against the competition?
FCUSA Polyaspartics offers 2x more floor value than epoxies and polyurea flooring with a true one-day return to service floor.
Floor Value is calculated by measuring what is left on the floor. When a resinous coating system is installed on a commercial or residential concrete floor, the measure of value is what is left when the floor coating system cures and is returned to service.
Let’s compare FCUSA Polyaspartics to other epoxy and polyurea floors.
FCUSA 100% Polyaspartics Flooring systems stacks up against the competition by providing superior adhesion, non-yelling, and 4x greater wear resistance. In addition, due to the quick recoat and return to service, the value remains on the floor.
Stacking the floor value from bottom to top , we learn the following:
Primer: First, after proper surface preparation and crack repair we apply 4 to 7 mils of the non-yellowing all-polyaspartic self-prime color coat that wets, wicks, and bonds to the concrete, and while still wet accepts the 4 to 5 mils color flakes being broadcast into it.
Adhesive Strength: Our bond strength is greater than the cohesive strength of the concrete itself. Adhesion strength >500 psi ASTM-d-4514.
Color Flakes and Yellowing: Since the layer of color flakes do not totally block UV rays, the primer color layer can yellow and discolor. This is a critical material selection because it’s generic resin composition determines if the total system will remain resistant to yellowing and discoloration from UV rays. Epoxies or polyurea primers are aromatic resins in chemical composition and will cause yellowing and discoloration when UV rays penetrate through the layer of color flakes. A 100% all polyaspartic self-prime product like FCUSA POLY SUPREME Polyaspartics is aliphatic in chemical composition and will not yellow or discolor underneath the color flakes.
Top Clear Coat: At the top of the floor system is a clear coat layer. FCUSA Polyaspartics offers 7–12 mils thickness. This clear coat gives a wear layer that is 4x greater than the wear and direct impact resistance of epoxies.
The value is left on your floor with FCUSA Polyaspartics
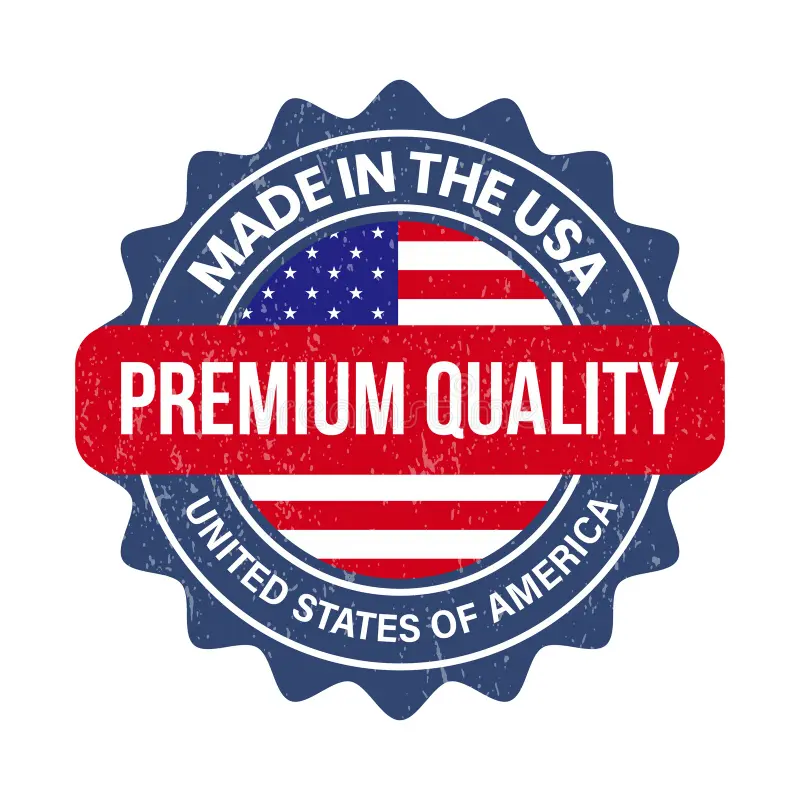
Why Is FCUSA POLY SUPREME Polyaspartics Different from Other Coatings?
- FCUSAPolyaspartics branded label is a Commercial/Industrial Quality system for residential garage floors
- Primer coat does not allow yellowing or discoloration underneath the flakes or chips from UV sunlight
- 6 hours from start of installation to finish then immediate return of belongings
- High direct impact and wear resistance 4x greater than epoxy
40% of cost is material that remains on the floor. Only 20% of the epoxy or polyurea system’s value remains on the floor - Adhesion to concrete greater than cohesive strength of concrete itself: Greater than 500.
- FCUSA labeled containers with 100% All Polyaspartic commercial/industrial coatings with technical and safety data sheets available
- Resistant to hot tire pickup
- Does not support the growth of bacteria or fungus
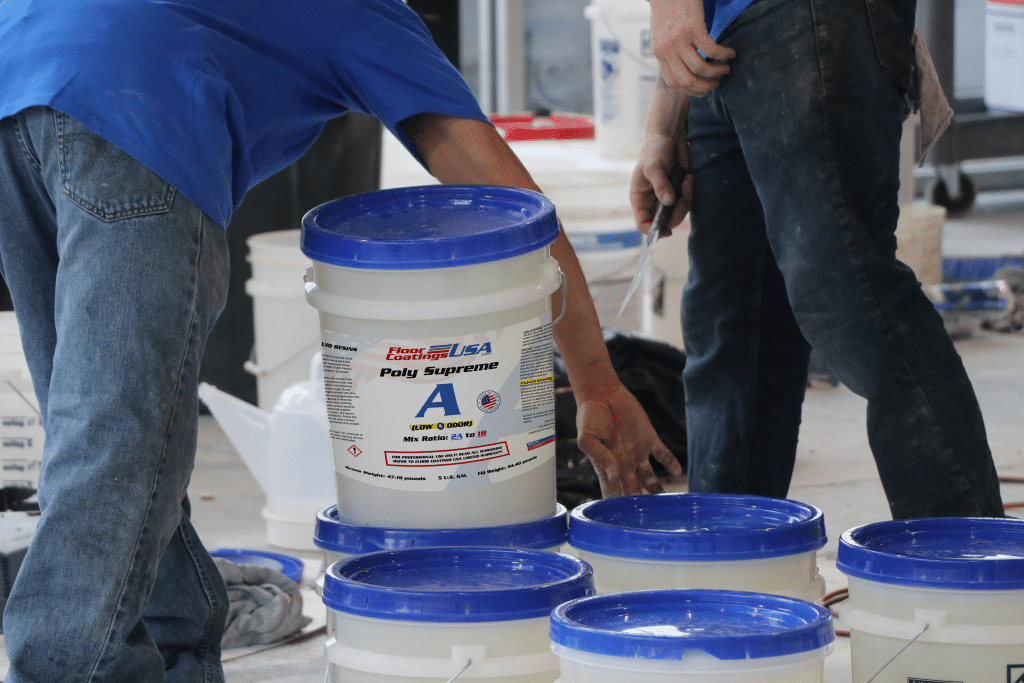
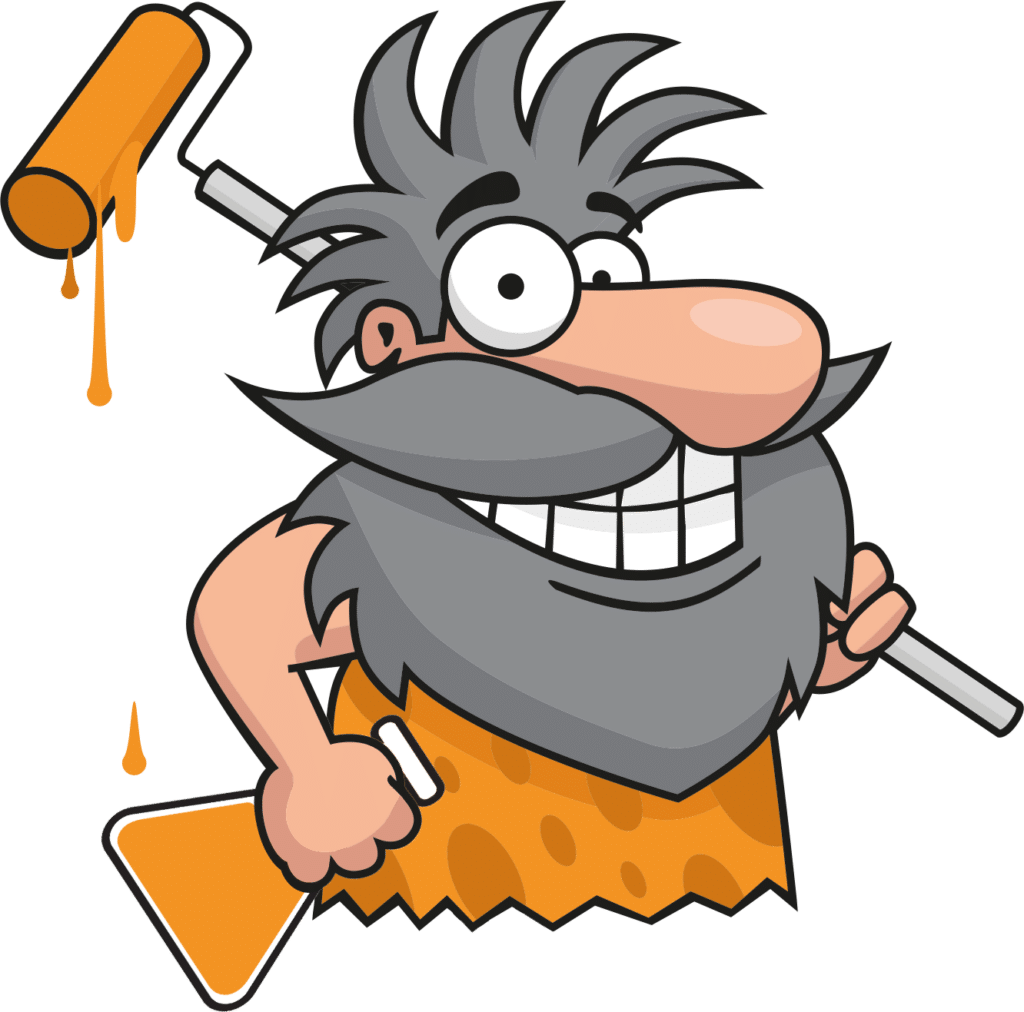
Tips from Carl the Chemist!
The answers center around performance properties, longevity of the coating, aesthetics, return to service and cost. Each impacts the owners in what they pay initially, how long it will last and what the aesthetics look like after 1 to 2 years and even 10 to 20!
So every home owner should ask themselves … what is most important? the lowest price or the highest quality coating system? Not always is the highest price the best quality system! We are proud of provide you with answers to all the questions you need to make an educated decision where your hard earned dollars are best spent!
Price competition is driving the initial installation cost downward. The only way to lower the price of a completed floor coating is to reduce the material cost and or lower the thickness of the coating. If lowest price is the owner’s objective, they have a choice between an epoxy/polyaspartic or polyurea/polyaspartic system. Remember the possible reasons behind lowest price are lower product cost of epoxy and polyurea because they are aromatic in chemical makeup and yellow and discolor which is why many are excluding yellowing and discoloration from their warranties. The epoxy and polyurea are the resinous part of the coating and they can be further modified with cheap plasticizers and other reactive resins.
The other is the colorant and pigment part of the coating representing cheap low-quality fillers that only increase the solids content. These consist of either talc (baby powder), calcium carbonate or barium sulfate and they detract from quality performance. To gain a competitive edge by having the lowest price, an epoxy or polyurea formulator can easily do the above and disregard quality. Remember the saying “You get what you pay for”. Another way to lower the selling price to the owner is to apply a thinner polyaspartic clear coat by 40 to 50% less.
Your Garage Cave can provide a free estimate or quick quote,
Many variables go into pricing: Location (distance from the shop), City, Size, Condition of concrete (new or old), any old epoxy coatings removal, cracks to repair etc. Your money is going towards a valuable product with less labor vs cheaper products and more labor hours.
An FC-USA all 100% polyaspartic coating system offers the greatest Floor Value for the owner. This Floor Value is the coating material cost that remains on the floor after the applicator leaves the premises. With the others there is a greater application cost and not the material left on the floor. For the assurance of a residential application to last for well over 20 years the owner can take comfort that a like-new appearance will remain over this length of time. This comes at just a slightly higher up-front cost, but over the years, the owner will not have to confront any yellowing and discoloration issues. An additional benefit to the homeowner is that they are getting a commercial-quality coating system for their residential garage floor.
Your Garage Cave leaves the value on the floor with 100% polyaspartic on both the base and the top, resulting in floors that are 30% Thicker than those of our competitors.
FC-USA Polyaspartic flooring performance is the highest in the industry, eliminating the need for expensive maintenance regiments.
No waxing, polishing, buffing, or resealing necessary! Clean with water and mild detergents for a long-lasting, beautiful floor.
NONE! Clear polyaspartic topcoats do not block or filter UV rays of sunlight. They will pass through and attack the epoxy and polyurea resin binders of the coatings. This is proven in a 500 hr study conducted by epoxy and polyurea pigmented primer coatings do yellow from UV rays of sunlight. They yellow, fade and oxidize leading to micro cracking and weakening their adhesion to concrete.
Absolutely for your Garage Floor coating, patios, driveways, walkways, and more.
An FC-USC floor you can walk on in a few hours; the garage door stays 6-12 inches overnight. You are ready to move in the next morning!
The biggest misconception is that a Polyaspartic (Aliphatic) over a Polyurea/Epoxy (Aromatic) is going to make that basecoat UV stable. 2. Epoxy and Polyurea have strong fumes which lingers. 3. Epoxy coatings take longer to harden. 4. Epoxy and Polyurea are temporary solutions. Yellowing and discoloration require replacing the floor and costly maintenance.
Hire Garage Cave because they exclusively use FC-USA floors for a true 100% polyaspartic coating. There are no hidden anything, no water barrier fees or extra costs, no recoat or resealing fees. No extra fees to store your belongings for several days, as a true polyaspartic floor on both base and top allows you to walk on it in just a few hours.
Your Garage Cave provides Value, Service and Quality to your home!
Yes. FC-USA has the highest level of solid content of a true Polyaspartic, 93%, which makes it thicker. There are hybrid polyaspartics that have been able to copy old school technology 2-1 ratio and a less than desirable number of solids.
This is important when learning the difference between Abrasion and Wear Resistance and how long your floor will last. Overall, polyaspartics on the base and top coat are the ideal choice for anyone looking to add Value to their home.
Yes, a true 100% FC-USA polyaspartic can be walked on in an hour in high humidity. Areas like Arizona 2-3 hours. See the chart for epoxy times or other Hybrid Polyaspartics.
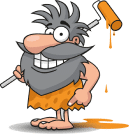
Absolutely NOT! FC-USA Polyapsartics are 100% Aliphatic, UV stable, and do not require additives to achieve a temporary fix. Polyurea and Epoxy are Aromatic, and if used on the basecoat, even with a polyaspartic over, will turn Yellow. The chemist provided a video to back up our comparisons.
No, never, get it done right the first time with YGC and do not risk having to REDO your floors and that added expense.
A finished FC-USA color flake floor is bright, glossy, and has just a slight texture to it. And the floor will retain its appearance—without yellowing or fading due to age or exposure to fluorescent lighting or sunlight—for years to come, with no buffing, polishing, waxing, or re-sealing.
Clients call Your Garage Cave and have us REDO Garage Floors every day due to failures of epoxy and polyurea.
Easy broom sweep, mop, or blow out, are the best care options. Unlike epoxy, a polyasparic floor will withstand power washing with no peeling. Dawn dish soap and water down simple green are the best supplies to clean a polyaspartic floor. Nothing harsh needed.
Our Top Rated FC-USA polyaspartic concrete coatings are virtually maintenance-free. Our coatings do not allow liquids to penetrate, for example, oils, kerosene, and gasoline. Paper towel clean up.
Yes, with FC-USA polyaspartic coatings, it is that simple! Using polyaspartic (aliphatic) on the base and the top to ensure colors will not fade or yellow with exposure due to age or exposure to sunlight or UV lighting. We offer coatings to beautify and enhance all your outdoor concrete, which have proven to last.
NOT RECOMMENDED: An Epoxy Garage Flooring or Polyurea basecoat is aromatic and will yellow and fade over time. Do not spend your time outdoors on the maintenance and repair treadmill with these products . . . spend it enjoying friends and family!
The highest quality FC-USA all-polyaspartic color primer/clear polyaspartic topcoat. FC-USA self-priming color coats only contain prime pigments, such as titanium dioxide, that provide the highest opacity and brightness. This pigment is UV-stable and, along with the all-polyaspartic aliphatic resin component, allows for both exterior and interior use.
Two major misleading statements are being made to residential garage homeowners.
One is that epoxy and polyurea pigmented coatings do not yellow when exposed to UV rays of sunlight.
Yes, epoxy and polyurea pigmented primer coatings do yellow from UV rays of sunlight. They yellow, fade and oxidize leading to micro cracking and weakening their adhesion to concrete.
The other is a clear polyaspartic topcoat will filter or block the UV rays and prevent yellowing.
No, clear polyaspartic topcoats do not block or filter UV rays of sunlight. They will pass through and attack the epoxy and polyurea resin binders of the coatings.
See QUV Study
FC-USA Polyaspartic coatings have self-priming, excellent penetrating, and bonding strength. Our floor coatings can be installed in temperatures anywhere between -30 degrees and 140 degrees Fahrenheit. This means that, except in very extreme environments, you can have our coatings installed any time of year, even in Arizona’s heat and Colorado’s cold.
We have perfected using the correct system for applying Polyaspartic Floor Coatings that involves prepping the floor, applying 100% polyaspartic on the base, throwing a full broadcast chip, within an hour or so, we are scraping the chips, vacuuming, and applying FC-USA 100% UV protective clear coat. NO EPOXY OR POLYUREA BASECOAT (aromatic) not UV stable!
Yes, FC-USA Coatings is once again revolutionizing the way coatings are applied in the shortest time possible, both in residential and commercial settings.
A polyaspartic is not a “do it yourself” application.
Hiring a professional is the best way to ensure that your flooring will look amazing and last a lifetime. FC-USA Polyaspartic flooring is easy to install by well trained, licensed employees of Your Garage Cave. But that’s not the most important feature. The key is the time it does not take for installation. Less time saves you time and money.
All the cheap do-it-yourself kits are not UV stable, take time, and are outperformed by the highest quality FC-USA all polyaspartic color primer/clear polyaspartic topcoat. FC-USA self-priming color coats only contain prime pigments, such as titanium dioxide, that provide the highest opacity and brightness. This pigment is UV-stable and, along with the all-polyaspartic aliphatic resin component, allows for both exterior and interior use.
Always require the seller to present proof of their product performance claims.
Yes, contrary to the misconceptions out there, epoxy and polyurea pigmented primer coatings do yellow from UV rays of sunlight. They yellow, fade and oxidize leading to micro cracking and weakening their adhesion to concrete. A Polyaspartic wicks into the concrete allowing for the best adhesion.
YES! Know what you are putting into your home! We do not cleverly confuse clients by giving vague misleading information about what product is being used on the basecoat even though the polyaspartic is on the top coat.
Our Chemist for Flexmar knows through countless studies formulators are making lower cost epoxies and polyurea’s by incorporating cheap pigment fillers in their formulations. i.e. talc (baby powder), calcium carbonate barium sulfate. Additionally, they are modifying the resinous epoxy and polyurea portions by adding cheaper diluents. These changes make the epoxies and polyurea’s lower cost per gallon but also weakens the color coat that is adhering to the concrete
Proud of having the best product in the coatings industry, FC-USA Polyaspartics for our base and top coat!
The highest quality FC-USA all-polyaspartic color primer/clear polyaspartic topcoat. FC-USA self-priming color coats only contain prime pigments, such as titanium dioxide, that provide the highest opacity and brightness. This pigment is UV stable and, along with the all-polyaspartic aliphatic resin component, allows for exterior and interior use.
Polyurea color primer/clear polyaspartic topcoat has excellent adhesion to concrete, physical properties and chemical resistance, easy to apply but shorter working times and lower cost because of their aromatic chemical make up. They yellow and discolor when exposed to UV rays. Their return to service could be the next day. Note: clear polyaspartic allows UV rays of sunlight to pass through, thus allowing the polyurea to yellow and discolor.
These floor coatings come with a lifetime warranty because they are expected to last you that long.
FC-USA Polyaspartic floor coatings are very damage-resistant and strong. They will not chip, and there is no hot-tire pickup, even on the hottest of days. They have the highest resistance to abrasion compared to Polyurea and Epoxy.
NO HOT TIRE PICKUP!
Your Garage Cave only uses the highest-quality products by FC-USA.
Our bond strength is greater than the cohesive strength of the concrete itself. Adhesion strength >500 psi ASTM-d-4514
A floor protected with FC-USA polyaspartic coatings will maintain its glossy, like-new appearance with only periodic dry sweeping and wet mopping with mild detergent as needed. That is it. There’s no regular, labor-intensive, costly maintenance… no stripping, no waxing, polishing, burnishing, or chemical deep cleaning that is endemic to ceramic or porcelain tile, VCT or sheet vinyl flooring, carpeting, and polished concrete.
Polyaspartic hands down. Our 93% solids Polyaspartic has High direct impact and wear resistance 4x greater than epoxy. Our coatings are 30% thicker in application giving our clients longer abrasion wear and tear, durability, quality, and service for over 20 years.
Another major benefit is: 40% of cost is material that remains on the floor. Only 20% of the epoxy or polyurea system’s value remains on the floor
Chemical differences make polyaspartics more versatile, more durable, and flexible compared to epoxies.
If your floor looks like this… Yellowing, hot tire pick up, peeling etc. you have been a victim of all the AROMATIC products on the market. An Epoxy, Polyurea, and Polyurethane are just a few. Polyurea is also used to coat truck bed liners as told by our competitors. Unfortunately, a different application and chemistry than floor coatings are currently used, which is why they are sprayed on in black; this is the only reason they do not yellow. Black is UV stable.
FC-USA all polyaspartic color primer/clear polyaspartic topcoat are Aliphatic (100% UV Stable). FC-USA self-priming color coats only contain prime pigments, such as titanium dioxide, that provide the highest opacity and brightness. This pigment is UV-stable and, along with the all-polyaspartic aliphatic resin component, allows for both exterior and interior use.
Many dealer -applicators claim their polyurea or epoxy coatings do not amber or yellow due to ultra violet light rays from the sun. This is contradictory to known technology so the purpose of this test is to demonstrate this fact. The chemistry of epoxy and polyurea coatings are aromatic in chemical composition and therefore are prone to amber and yellowing from UV sunlight. The chemistry of polyaspartic coatings is aliphatic in chemical composition and is not prone to ambering and yellowing from UV sunlight.
At this point it should be mentioned that this segment of the market has grown quickly and is now hampered by individuals who lack knowledge of coatings technology. They make claims to owners that have no technical basis and no back up data for the coatings they are promoting just to make a sell. Many of the coating’s products are private labeled with no mention of the actual manufacturer.
Polyaspartic Concrete coating is another name for Aliphatic Polyurea, which is a hybrid material consisting of ester and other materials. It was originally developed to coat metal bridges. It was later used to coat concrete flooring due to its durability and moisture resistance.